Introduction
『QC7つ道具』は、「どこから手をつければ良いのか分からない」という状態から、問題点や優先順位を明らかにし、解決の方向性を定めるために活用する手法です。
ITシステムが社会やビジネスを支える基盤となった現在、ITシステムの品質管理は欠かすことのできない活動です。一方でITシステムの急激な拡大・複雑化に伴い、品質管理者は高度化、複雑化する諸課題への対応が求められています。みなさまのなかにも、現場に山積する品質課題を前に「どこから手をつければ良いのか分からない」と頭を抱えた経験をもつ方もいらっしゃるのではないかと思います。長年お客様の品質保証を支援してきた弊社でも、システム開発の現場での対応に苦戦を強いられることは少なくなく、品質管理者に対する要求の高度化、複雑化を日々実感しています。今回紹介する『QC7つ道具』は、そのような悩み多き品質管理担当のみなさまの一助になるものと考えております。
まだ活用したことがない方はぜひ参考にしてみてください。
目次
QC7つ道具とは?
QC(Quality Control:品質管理)は、もともと日本の製造業で広がってきたものです。日々、大量の製品が生産される製造の現場では、廃棄ロスやムダの削減、リコールのような大問題を回避するため、製品の品質を一定の水準に保つことが求められます。そのため、日々現場で蓄積されるプロダクトに関わるデータを収集し、統計的な分析や管理、改善活動を組み合わせて品質の向上を図る活動を徹底して行う必要があります。このような一連の品質管理の取り組みをQC活動と呼びます。QC活動のなかで分析や改善のために活用されている手法がQC7つ道具です。
QC7つ道具には『QC7つ道具』と『新QC7つ道具』の2種類存在します。
『QC7つ道具』は、製造工程や品質などに関する定量的なデータを整理・分析するための手法で、『新QC7つ道具』は数値化が難しい特性や要因といった定性的なデータを整理・分析するための手法です。
以下で『QC7つ道具』『新QC7つ道具』それぞれの手法について解説します。
QC7つ道具の種類
パレート図
項目別に数値を大きい順に並べた棒グラフと各項目の累積構成比を示した線グラフによって構成されている複合グラフ。発生している問題全体のなかで大きな影響を占めるものが何かを明確化し、重要な問題を特定するための手法。2:8の法則で有名なあの「パレートの法則」に基づくものです。
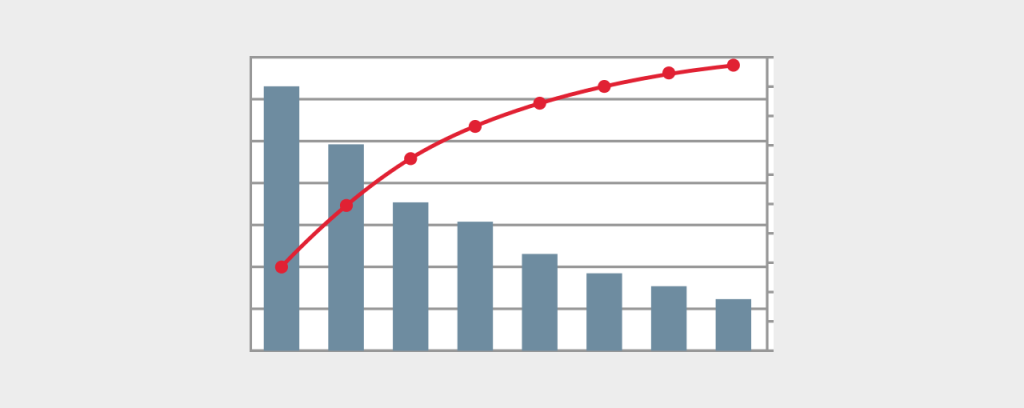
特性要因図
特性と要因の関係を系統的に線で結んで(樹状に)表した図のこと。結果である特性がどのようにしてもたらされたかを要因と結び付けて図式化し、そこに潜んでいる問題点を炙り出すのに用いられる手法。フィッシュボーン図として有名。
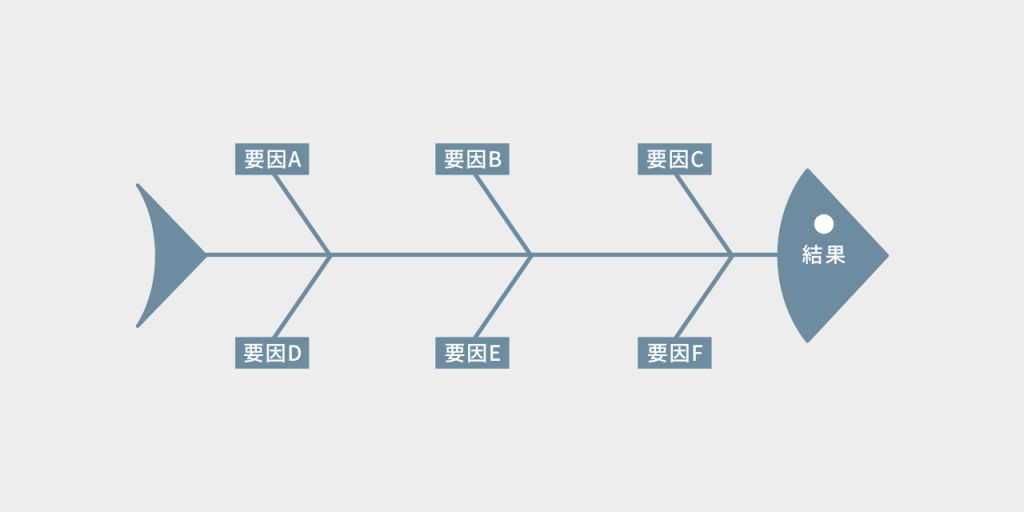
グラフ
データを視覚的に表現し、変化や比率を把握しやすくしたもの。棒グラフや折れ線グラフ、円グラフなどさまざまな種類がありますが、グラフに関しては多くの人が日頃から活用されているのではないかと思います。
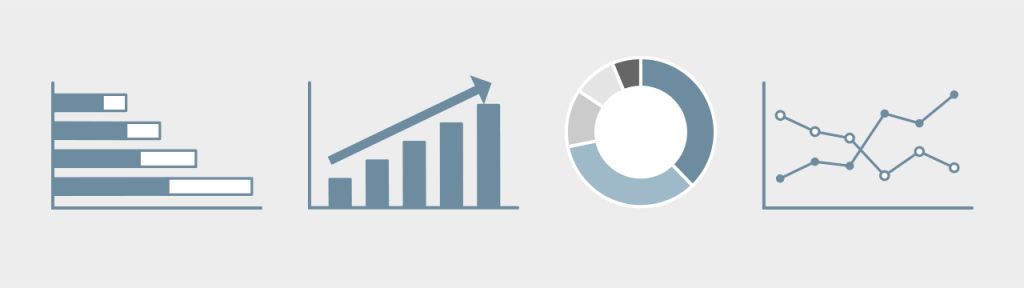
ヒストグラム
データの分布状態を視覚的に把握するための統計グラフ。棒グラフに似ていますが、それぞれの値が独立している棒グラフに対して、ヒストグラムは全ての数値が集まることで傾向を表現します。データの分布傾向や偏りを把握することで全体的な問題を見つけるために用いられる手法。
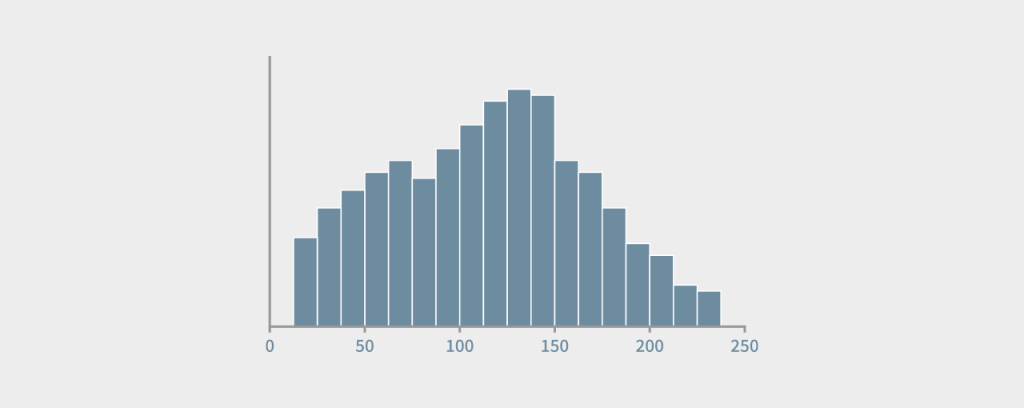
散布図
縦軸と横軸に量や大きさを取り、データを2つの項目の当てはまる箇所にプロットしたグラフ。グラフ上の点の散らばりで2項目間の相関関係の有無を判断することを可能とし、要因と特性の相関関係を確認する際に活用される手法。
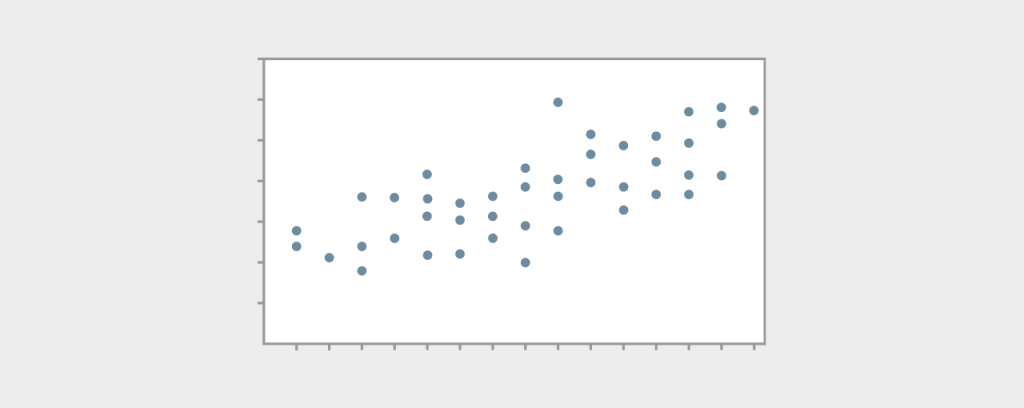
管理図
目標値を中心線に上方管理限界線と下方管理限界線を配置し、時系列の状態変化を表現する折れ線グラフ。管理範囲内のデータ変化の把握と、管理限界線を逸脱したデータの有無から異常発生の検知が可能。工程などの管理状態を視覚的に把握するために用いられる手法。
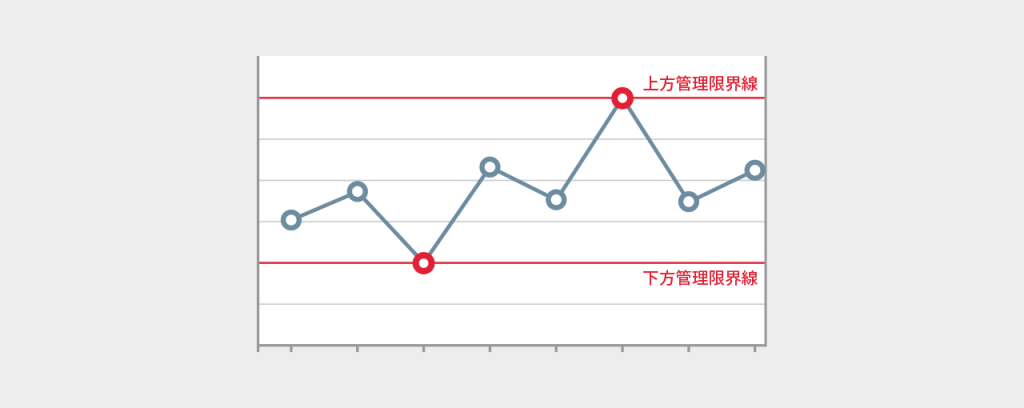
チェックシート
あらかじめ決められた確認項目に対してOK/NGの判断を記入する表。大量の点検や確認項目を漏れなくチェックすることが可能となり、確認結果のデータ収集を容易にします。現場で発生した問題および不良を記録し、現状把握、解析、点検を効率的に行うための手法。
新QC7つ道具について
親和図法
親和図法とは、まとまりのない言語データをデータ間の親和性によって整理・分類し体系化する手法です。混沌として状況が整理されていない時や、取り組むべき課題が明確でない時に使います。似たもの同士をまとめながら整理していくことで、問題の全体像、構造、ポイントが把握でき、取り組むべき課題が明確になります。KJ法という名称で有名。
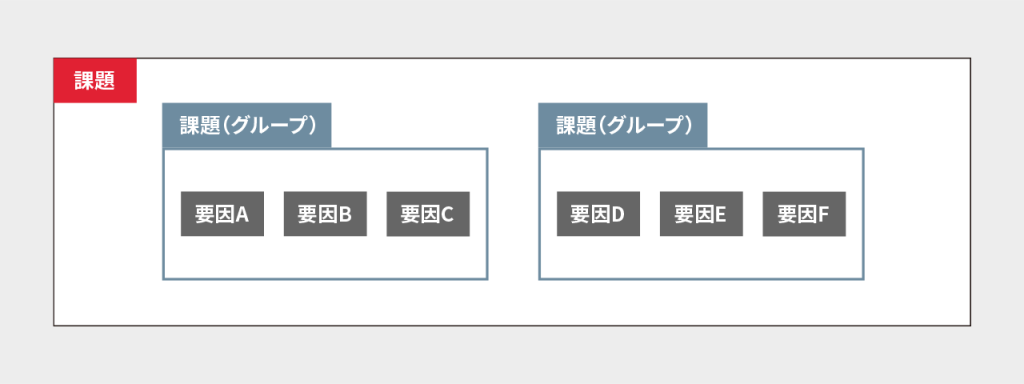
連関図法
連関図法とは、「原因」と「結果」、「目的」と「手段」などが複雑に絡み合った問題について、その要素間の関係を矢印でつなぐことで可視化し、問題要素間の因果関係を明らかにする手法です。因果関係を解きほぐすことにより原因を探すことが出来ます。
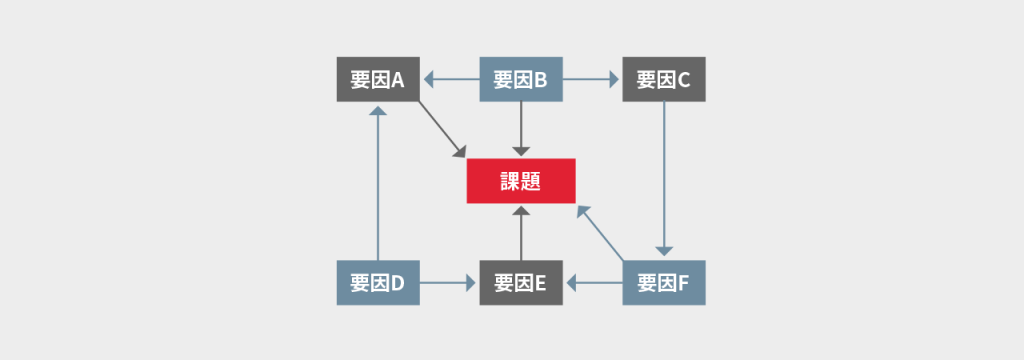
系統図法
系統図法とは、問題解決の「原因」と「結果」、「目的」と「手段」といった関係性を系統的に整理して問題解決の具体策を見つける手法です。最終ゴールとなる目的を頂点に設置し、それを実現するための手段を階層的にブレークダウンすることで実行すべき手段の具体化を図ります。プロジェクト管理で活用されているWBSも、プロジェクトという目的を実現するためのタスクを系統的に分解しているという意味において系統図法と言えます。
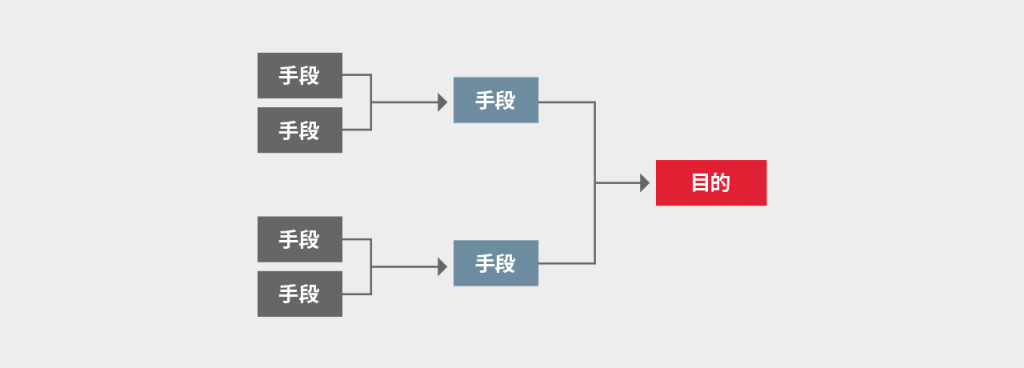
マトリックス図法
マトリックス図法とは、複数の要素を「行」と「列」の二次元に配置し、要素の交点に関係の有無、関連の程度を表示し、問題解決を効果的に進める手法です。マトリックス図法は、重要項目の洗い出しに優れており、「系統図法」によって展開した方策の「優先順位付け」などを決めるために使用されます。
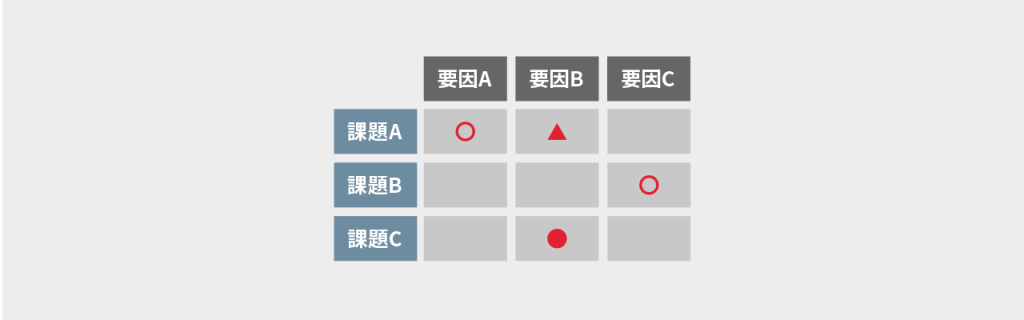
アローダイアグラム法
アローダイアグラム法とは、複数の独立した作業を並行して実施する際に、作業間のつながりと要する日数を図形と数値で可視化しながら日程計画を立てるための手法です。クリティカルパスを明確化し最適な日程計画を作成することが出来ます。一般的にPART図と呼ばれています。
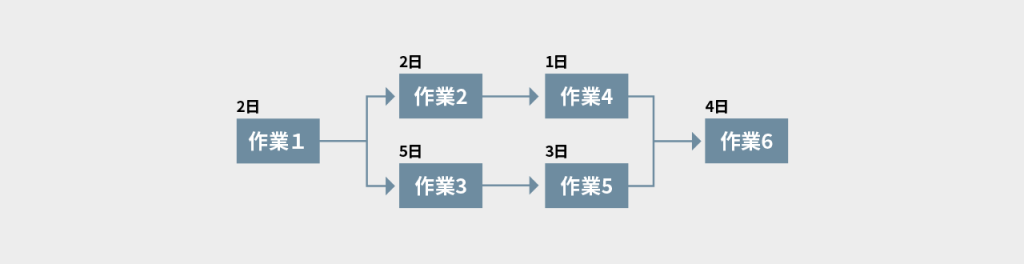
PDPC法
PDPC法とは、「Process Decision Program Chart」の略で、日本語では「プロセス決定計画図」と言います。目標達成までの過程を図示し、過程の中で予測されるリスクを明確化することで予め対応策を講じておくことための手法です。
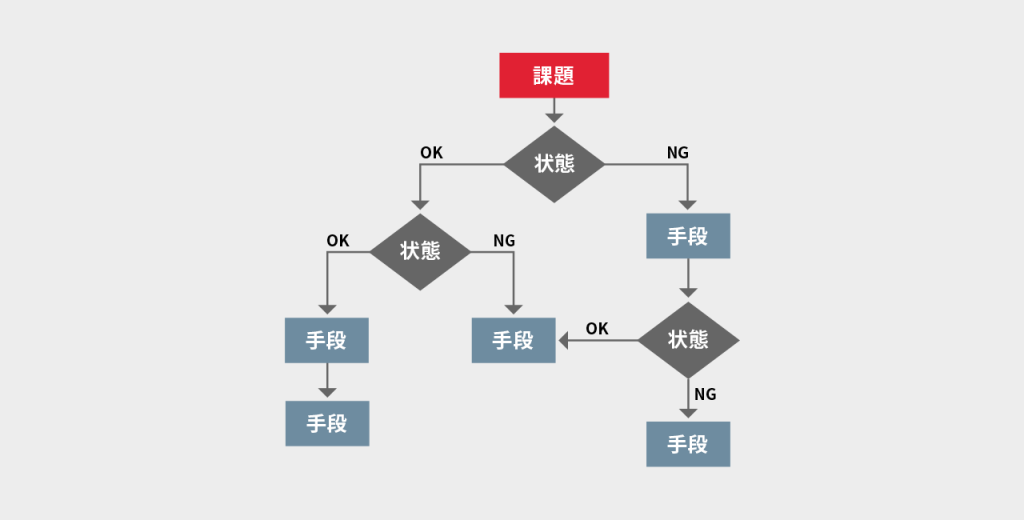
マトリックスデータ解析法
マトリックス形式に整理されたデータ群から、傾向、データ相関の有無を数値的に可視化し、現状を定量的に把握するための手法です。全要素中の個々の要素の位置づけを考えることで、個々の要素に含まれる傾向を数値化することが可能となり、複数の要素を整理することができます。『新QC七つ道具』の中で、唯一数値データを取り扱います。『QC7つ道具』の散布図と併用して用いられます。
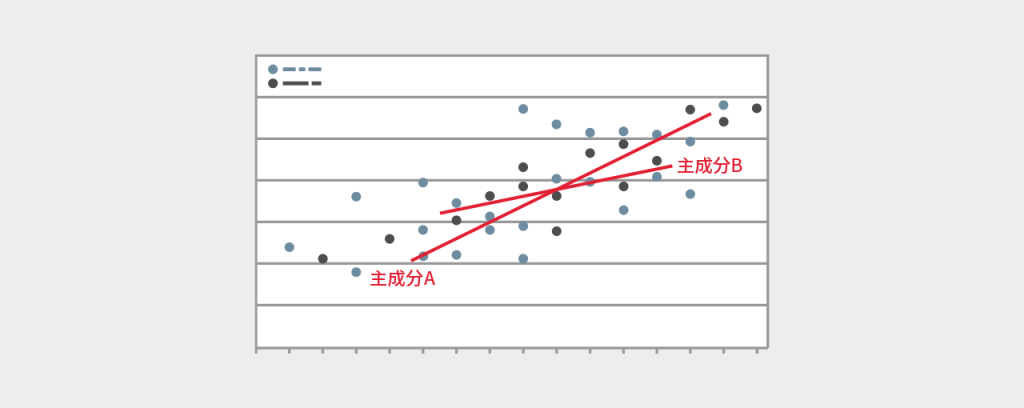
QC7つ道具を活用するQCストーリーについて
『QC7つ道具』『新QC七7つ道具』の概要を理解頂いたところで、実際のQC活動においてどのような場面で活用されるかを簡単にご紹介します。QC活動における問題解決は『QCストーリー』に則って進められ、『QC7つ道具』『新QC七つ道具』は『QCストーリー』の各ステップのなかで登場します。
『QCストーリー』の各ステップの内容と、各ステップで主に使用するQC7つ道具を以下にまとめます。
PDCA | STEP | 実施内容 | 主に使用する7つ道具/新7つ道具 |
Plan |
テーマ選定 |
改善対象のテーマ選定とその理由を |
パレート図、グラフ |
マトリックス図法 |
|||
現状把握と |
データを収集・分析して現状を把握し |
パレート図、グラフ、 |
|
親和図法 |
|||
活動計画 |
誰が、どのように、いつまでに |
グラフ |
|
アローダイアグラム、PDPC法 |
|||
要因解析 |
特性と要因の因果関係を明らかにし、 |
ヒストグラム、特性要因図、 |
|
系統図法、 |
|||
対策立案 |
要因解析に基づき対策の実施方法を |
特性要因図 |
|
マトリックス図法 |
|||
Do | 対策実施 |
対策を実行する |
― |
Check |
効果確認 |
対策の効果を確認し、定量・定性的に |
チェックシート、管理図、 |
マトリックスデータ解析法 |
|||
Action | 標準化と 管理の定着 |
効果の維持・横展開できるよう標準化を図る |
チェックシート |
親和図法、連関図法 |
表1:QCストーリーで活用するQC7つ道具
QC管理活動において『QC7つ道具』を活用するポイント意義
以上の説明から、みなさまどのような感想をもたれたでしょうか?前向きに受け取る方もいる一方で、ネガティブな印象を抱かれた方もいるのではないでしょうか?
「改めて古典的な手法を取り入れても、現場の実情を一番把握している自分たちがこれまで考え尽くしてきたこと以上の発見は得られないのでは?」
私たちがお客様の依頼を受けて品質改善の支援をする際も、このような意見をいただくことは少なくありません。
では、実際に私たちがQCストーリーに基づいて対策立案を実施しても、お客様側の現場メンバーが考えてきた対策と同じ結論に至るのかと言うと、そうなることはほとんどありません。しかしながら、お客様側のQC活動メンバーのスキルや進め方に問題がある訳でもありません。それではなぜ、異なる結論に至るかというと、現場メンバーのなかで芽生えた手間や時間のかかる対策への抵抗感から、自然と手っ取り早い方法を選んでしまう「認知バイアス」がかかってしまうことが要因のひとつだと考えます。また、「認知バイアス」がかからなくても、Q(品質)C(コスト)D(納期)がトレードオフとなる状況下で、価値観が相違するステークホルダー間の合意形成を図るという困難を極める作業のなかで、立場の強い人の意見に引き寄せられる「同調圧力」に押されてしまうということもあると思います。
こうした「認知バイアス」や「同調圧力」といった非合理的な根拠に基づく判断が下されてしまうと、結果的にバランスを欠いた活動に陥ってしまいかねません。こういった状況を打破するためにも、統計的な分析や管理を行い明確な根拠に基づく合理的な判断を下し、改善活動を組み合わせて品質向上を図る活動が必要となってくるのです。
問題 | ・複合条件組み合わせで発生するイレギュラーケースの考慮不足によるシステム障害が頻発している状況 |
お客様が考えた原因 | ・有識者レビュー無し ・テスト不足 |
お客様が考えた対策 | ・有識者レビューを増やす ・「べし集・べからず集」に今回障害となったケースの条件を追記 |
SHIFTが指摘した対策の問題点 | ・有識者依存は有識者がボトルネックとなる(事実有識者不足が深刻な課題となっていた) ・個別ケースを積み上げた「べし集」「べからず集」は、確認事項が膨大となり手が回らなくなる ・流出原因のみに着眼し、混入原因を抑えようとしていない |
認知バイアスがかかる |
・顧客の要求は複雑すぎて可視化が困難。有識者知見に頼らざるを得ないという諦め感 ・混入原因の対策(要件定義や基本設計書の精度UP)は手間がかかるという負担感 ・これまでの問題点を指摘してきたが変わらなかったので、これからも変わらないという無力感 |
表2:認知バイアスが働く現場の状況の例
以下は、上記認知バイアスが働く現場の品質分析をSHIFTが特性要因図とマトリックス図法を活用して行った例。
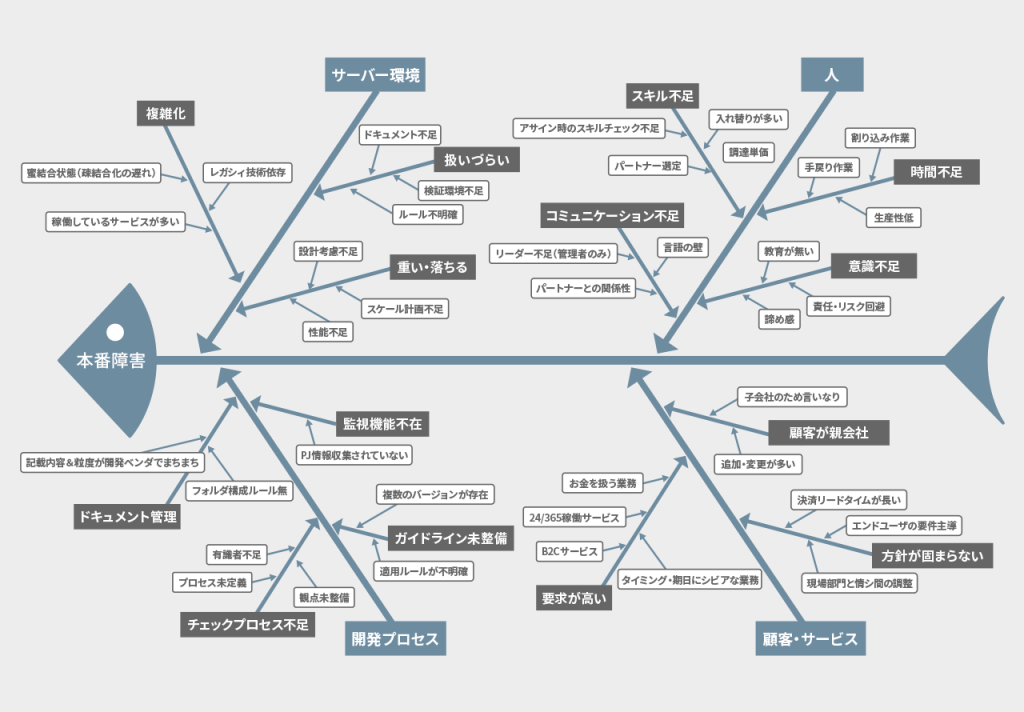
図1:上記認知バイアスが働く現場の品質分析をSHIFTで行った例(特性要因図)
※混入工程比率を分析
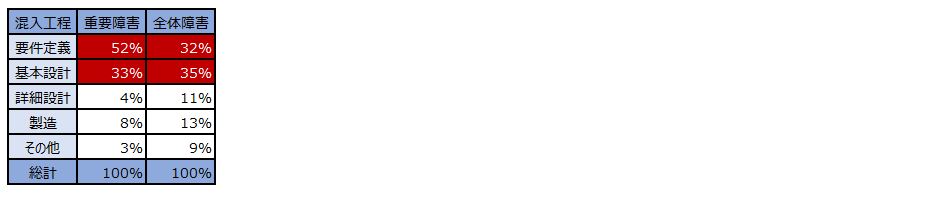
※要件定義、基本設計の中でさらに問題個所を特定

図2:上記認知バイアスが働く現場の品質分析をSHIFTで行った例(マトリックス図法)
まとめ
『QC7つ道具』『新QC7つ道具』、またそれらの活用について解説しました。これらはITシステムの品質管理において、問題点の発見や解決策の検討などに活用することができる手法です。本コラムでは「認知バイアス」についても触れましたが、現場では、気づかないうちに非合理的な判断をしているケースがあります。客観的に、明確な根拠に基づく判断をするという意義を踏まえ、この『QC7つ道具』『新QC7つ道具』を活用頂き、品質管理にお役立ていただければと思います。